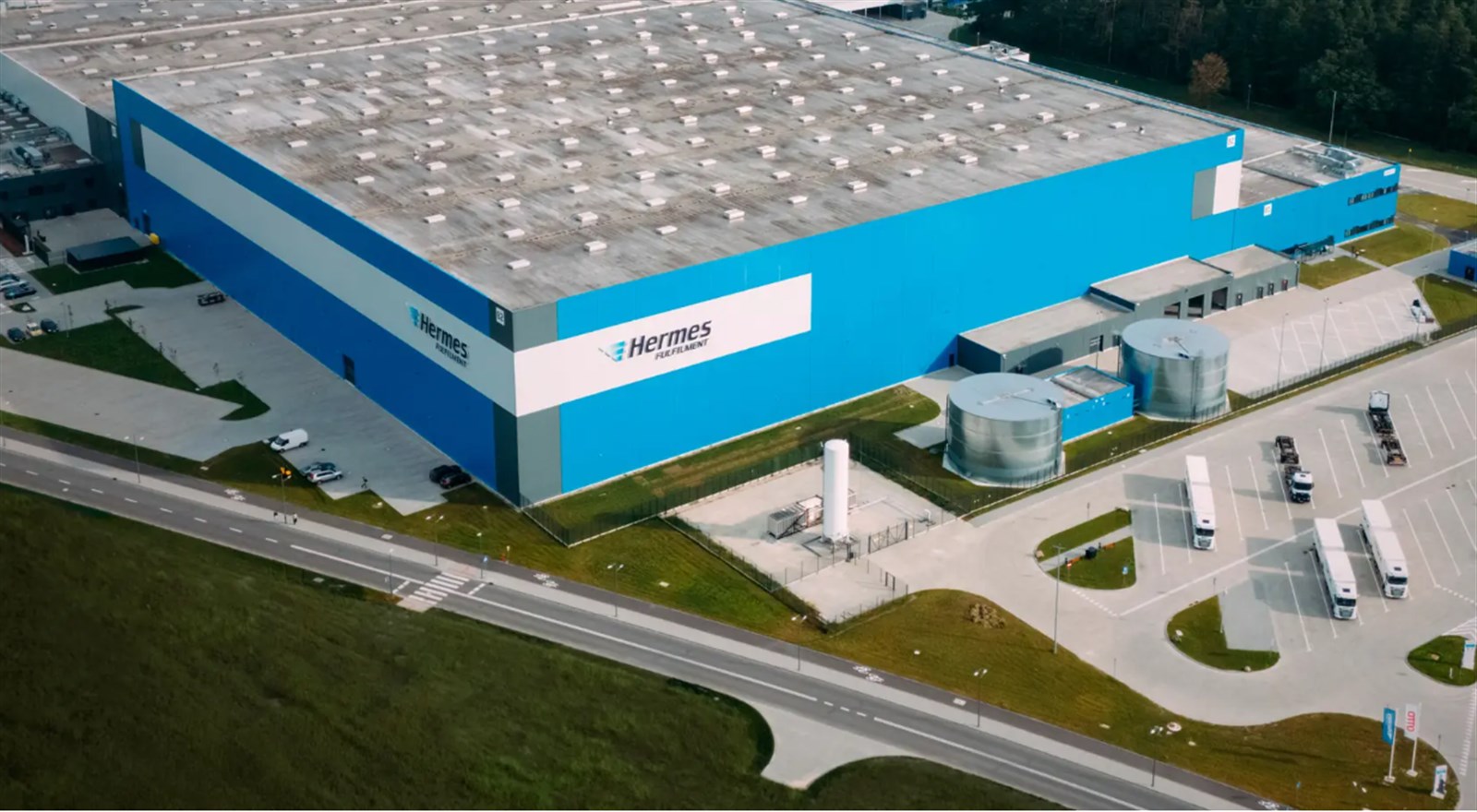
Gigantic – this term best describes the new distribution center in Iłowa. Located on the outskirts of the small town in western Poland, about an hour's drive from Cottbus, Germany, it has become a hub for e- commerce that is unparalleled.
A beacon project in European e-commerce - that seems like a valid description for the new logistics center in Iłowa. And this is not only due to the state-of-the-art so-called "pocket sorter", which literally puts orders into pockets and serves as the centerpiece of the facility. “With this forward-looking location, we will set standards across Europe,” says Kay Schiebur, a member of the Otto Group's executive board responsible for services. In terms of dimensions alone, the distribution center in Iłowa sets benchmarks. On a property covering approximately 260,000 square meters, roughly the size of 37 soccer fields, a building complex of nine halls has been constructed in just under two years, designed according to the criteria of the German Sustainable Building Council (DGNB), with a total floor area of around 118,000 square meters. This means that the total area of the building alone is equivalent to 16 soccer pitches. The usable area exceeds 268,000 square meters, more than double the size, as additional intermediate levels have been added in the picking area.
The Otto Group has invested a mid-three-digit million amount in the distribution center, aiming to elevate logistics for the online retailer OTTO to a new level and further increase speed in e-commerce.
Logistics from the Heart of Europe for Tomorrow's E-Commerce
The largest B2C location in Poland is operated by Hermes Fulfilment, a logistics service provider belonging to the Otto Group. The company will manage warehousing, packaging of online orders, and European shipping with up to 1,900 employees for OTTO. “The location in Iłowa is the first in our company’s history that we have completely planned and built from scratch abroad,” says Kevin Kufs, CEO of Hermes Fulfilment. The distribution center is tailored for the logistical handling of small-volume assortments, primarily clothing.
While the exterior of the complex is impressive due to its size, the interior primarily stands out for its cutting-edge technology and perfectly coordinated logistical processes. The goods receiving area features 28 gates, more than any other location operated by Hermes Fulfilment. Following a randomly sampled quality inspection, the delivered boxes with new goods enter the fully automated high-bay warehouse, which offers 1.2 million storage spaces across 26 aisles. Conveyors transport the boxes from the high-bay warehouse to the picking area, where employees gather the ordered items across 127,000 square meters. Larger or heavier products are often delivered on pallets, for which a manual narrow-aisle warehouse with a capacity of 33,000 pallet spaces has been specifically created. The picking of larger, heavier, and frequently ordered items is also done separately. This area spans a total of 40,000 square meters and accommodates 14,000 pallets. The arrangement over four levels saves valuable ground space, as load carriers with heavy goods are placed side by side on the floor for picking.
High Degree of Automation for Increased Speed
The centerpiece of the new distribution center is the aforementioned high-performance pocket sorter, which Hermes Fulfilment is using for the first time at a location. The pocket sorter connects the picking area with the hall where the ordered items are packaged for customers. Like a roller coaster, the sophisticated system winds predominantly overhead to the 90 packing stations in shipping. The installation above the employees' heads also saves valuable floor space for other uses. The ordered items are transported in 50,200 pockets at a speed of half a meter per second, regardless of whether products like shoes are packed in boxes or T-shirts in bags. Items must not weigh more than seven kilograms. The pocket sorter can transport up to 18,000 items per hour. Returned items are stored in a modern dynamic shuttle warehouse with 92,000 spaces.
The final stop on the journey through the distribution center, along the approximately eight-kilometer conveyor route, is the goods dispatch area. Here, the packed shipments are assigned to various shipping destinations using another sorting system and loaded onto waiting trucks at 98 gates. Deliveries primarily go to Germany, France, Austria, and the Netherlands. Up to 110 million shipments per year can thus be dispatched to customers.
Faster Deliveries, Improved Shopping Experience
It takes just under four hours for an ordered item to complete the entire process at the Iłowa distribution center. “The high degree of automation helps us to become significantly faster and to increase the so-called next-day delivery rate significantly,” emphasizes Kay Schiebur. The goal is to deliver at least 60 percent of orders by the following day. “The shorter delivery times will noticeably enhance the shopping experience,” the executive board member is convinced. “Speed and service have become crucial competitive factors in e-commerce. That’s why we continuously invest in new technologies and adapt our logistics network to reach our customers even faster,” says Kay Schiebur.
As in all areas of logistics, a good interplay between humans and machines is essential to meet customer needs and provide all colleagues in the logistics sector with a future-oriented working environment. That’s why the Otto Group relies on cutting-edge technology, artificial intelligence, and robotics at its logistics locations (read more here).
Since the end of July, the distribution center in Iłowa has been gradually ramping up operations. The warehouse is filling up, and operational activities have begun. Next year, the most modern logistics location in the Otto Group network is expected to operate at full capacity.